Production can utilize forecasts to make decisions concerning – Production forecasts are an indispensable tool for businesses seeking to optimize operations, reduce costs, and enhance customer satisfaction. By leveraging accurate forecasts, production teams can make informed decisions concerning production planning, inventory management, resource allocation, quality control, supply chain management, sales and marketing, and financial planning.
In this comprehensive guide, we delve into the myriad ways production forecasts empower businesses to achieve operational excellence. We explore practical examples, proven strategies, and the tangible benefits of utilizing forecasts to drive informed decision-making across the entire enterprise.
Production Planning
Forecasts provide valuable insights that enable production to make informed decisions regarding production schedules. By understanding future demand patterns, production can optimize its schedules to meet customer requirements while minimizing production costs. For instance, if a forecast indicates an upcoming surge in demand for a particular product, production can adjust its schedule to increase production levels accordingly, ensuring timely delivery and customer satisfaction.
Inventory Management
Forecasts help production manage inventory levels effectively. By accurately predicting future demand, production can maintain optimal inventory levels, reducing the risk of stockouts or excess inventory. Strategies such as just-in-time inventory management rely heavily on forecasts to ensure that raw materials and finished goods are available when needed, minimizing storage costs and waste.
Additionally, forecasts help production optimize inventory turnover rates, indicating the efficiency of inventory management practices.
Resource Allocation
Forecasts guide production in allocating resources efficiently. By anticipating future demand and production requirements, production can plan for and allocate resources accordingly. For instance, if a forecast predicts an increase in production volume, production can hire additional staff or invest in new equipment to meet the increased demand, ensuring smooth operations and timely delivery.
Quality Control
Forecasts can be used to identify potential quality issues. By analyzing historical data and trends, production can identify products or processes that are prone to quality defects. This information enables production to implement preventive measures, such as enhanced quality control inspections or process improvements, to minimize the risk of quality issues and ensure product quality.
Supply Chain Management
Forecasts play a crucial role in supply chain management. By providing insights into future demand, production can effectively manage its supply chain, ensuring timely delivery of raw materials and components. This collaboration with suppliers helps maintain stable production schedules, reduce lead times, and enhance overall supply chain efficiency.
Sales and Marketing
Forecasts inform sales and marketing strategies. By understanding future demand patterns, sales and marketing teams can target specific customer segments, develop targeted marketing campaigns, and plan product launches accordingly. Accurate forecasts help sales teams set realistic sales targets, while marketing teams can tailor their campaigns to meet specific customer needs, driving sales growth and brand loyalty.
Financial Planning, Production can utilize forecasts to make decisions concerning
Forecasts aid in informed financial decisions for production. By anticipating future demand and production costs, production can optimize its production budget. Forecasts help identify potential financial risks and opportunities, enabling production to allocate funds strategically, invest in new technologies or products, and ensure financial stability.
FAQ Corner: Production Can Utilize Forecasts To Make Decisions Concerning
How can forecasts improve production schedules?
Forecasts provide visibility into future demand, enabling production teams to adjust schedules proactively, minimize downtime, and ensure efficient resource allocation.
What strategies can businesses employ to reduce inventory costs using forecasts?
Forecasts help businesses optimize inventory levels by identifying optimal reorder points, reducing overstocking and minimizing carrying costs.
How do forecasts guide resource allocation decisions?
Forecasts provide insights into future capacity requirements, allowing production teams to plan for workforce management, equipment utilization, and material procurement effectively.
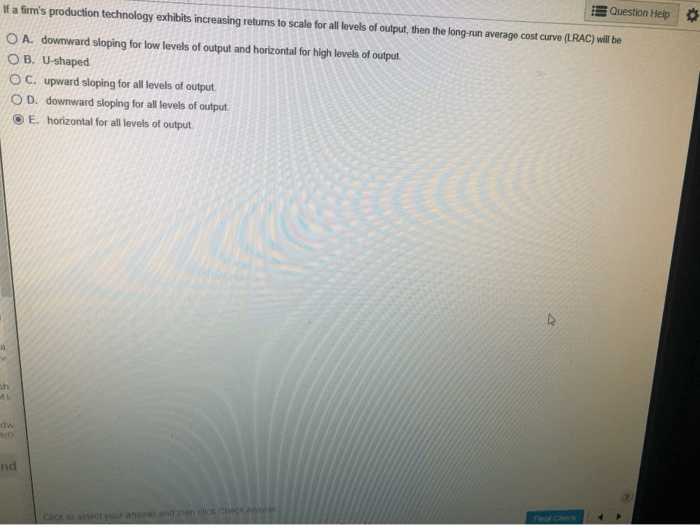
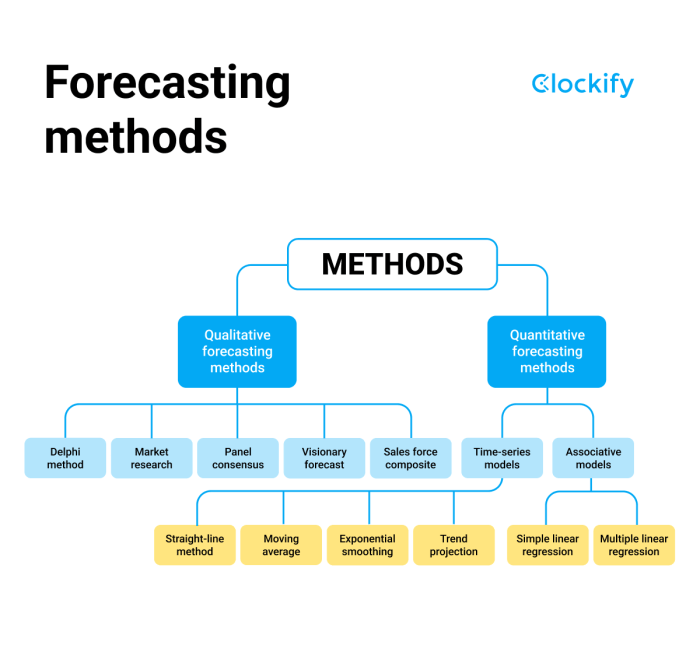
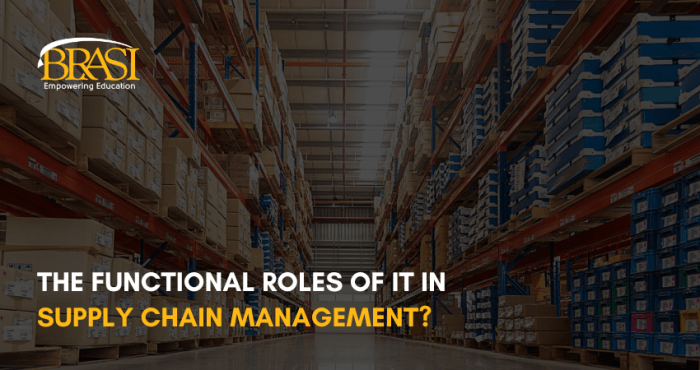